Polymethyl methacrylate (PMMA) is a transparent thermoplastic that is known for its optical clarity, weather resistance, and excellent impact strength. Often referred to by brand names like Plexiglas, Lucite, and Acrylite, PMMA is widely used in industries ranging from automotive to medical applications. In this comprehensive guide, we will explore the properties, manufacturing processes, uses, advantages, and potential drawbacks of PMMA. We will also dive into its search popularity and practical benefits, based on user searches on platforms like YouTube and Google.
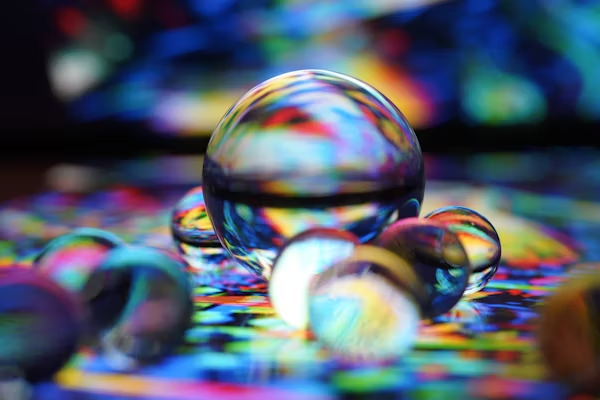
What is PMMA?
PMMA is a synthetic polymer of methyl methacrylate, an ester made from methacrylic acid. It’s commonly known as acrylic, acrylic glass, or simply as a type of “plastic” due to its widespread use and versatile properties. While it is most recognized for being a clear, rigid material, PMMA can be made in different colors and finishes, depending on the intended application.
Chemical Structure and Characteristics of PMMA
The chemical structure of PMMA consists of long chains of methyl methacrylate monomers. These chains are polymerized to form a solid, thermoplastic polymer. The key characteristics of PMMA include:
High Optical Clarity: PMMA is often used as a substitute for glass because it is highly transparent, with a light transmittance of up to 92%, which makes it an excellent choice for applications requiring high clarity.
UV Resistance: It has natural resistance to ultraviolet (UV) radiation, which means it is not easily degraded by exposure to sunlight. This feature makes it ideal for outdoor applications.
Impact Resistance: Though PMMA is more brittle than other plastics like polycarbonate, it still offers reasonable resistance to impact. This is enhanced when it is manufactured with specific additives or in combination with other materials.
Weather Durability: It maintains its appearance and performance over time, even when exposed to harsh weather conditions. It does not yellow or lose its clarity easily.
How is PMMA Made?
It is typically produced using either bulk polymerization or suspension polymerization methods. The production process begins with the creation of methyl methacrylate monomers, which are polymerized to form PMMA. These methods result in a variety of forms, from cast acrylic sheets to extruded versions of the polymer.
Bulk Polymerization
In bulk polymerization, the monomer is heated in the presence of an initiator, and the reaction leads to the formation of long polymer chains. This method often produces high-quality PMMA with fewer impurities, making it suitable for optical and high-performance applications.
Suspension Polymerization
In suspension polymerization, methyl methacrylate is suspended in water, with the polymerization taking place in small beads. This method is typically used to produce larger volumes of It and is more suitable for applications requiring extruded or molded plastic.
Types of PMMA and Their Uses
It is not just one standard material. It can be manufactured in several different forms, each tailored to specific applications. Some of the most common types of PMMA include:
Cast Acrylic
Cast acrylic is produced by pouring liquid methyl methacrylate into a mold, where it hardens into a solid sheet. This method results in superior clarity and a smooth surface, making it a top choice for decorative applications such as displays, signs, and lighting.
Extruded Acrylic
Extruded acrylic is produced by forcing the polymer through a mold to form sheets, rods, or tubes. While it is not as optically clear as cast acrylic, it is more affordable and easier to produce in large quantities. It is commonly used in general-purpose applications like furniture, glazing, and automotive parts.
Colored and Textured Acrylic
In addition to clear acrylic, PMMA can be produced in a wide variety of colors and textures. Colored It is frequently used in signage, decorative elements, and automotive parts, while textured acrylic is often used for privacy screens, lampshades, and architectural panels.
Applications of PMMA
PMMA’s versatility makes it applicable across various industries, from construction to electronics. Let’s explore some of its most popular applications.
PMMA in the Automotive Industry
The automotive sector relies heavily on It due to its combination of strength, optical clarity, and impact resistance. It is used in:
Headlights and Taillights: It deal for automotive lighting due to its transparency and UV resistance, which helps prevent yellowing over time.
Windows and Mirrors: It is also used for side windows, mirrors, and sunroofs, as it is lighter than glass, reduces weight, and offers a similar clarity.
Dashboard Components: The lightweight nature and durability of it make it perfect for dashboard covers and other interior components in vehicles.
PMMA in Architecture and Construction
PMMA is a popular material in the construction industry for its aesthetic appeal and physical properties. It is used in:
Windows and Glazing: Due to its weather resistance and optical clarity, PMMA is often used as a glazing material in building facades, skylights, and windows.
Lighting Fixtures: PMMA is often molded into various shapes for lampshades, light diffusers, and architectural lighting, enhancing the visual appearance of both interior and exterior spaces.
In Summary
Polymethyl methacrylate (PMMA) is a versatile and durable polymer with applications across numerous industries, including automotive, medical, architectural, and consumer products. Its optical clarity, impact resistance, weather durability, and ease of processing make it an ideal material for many applications that require strength, appearance, and longevity.
While it has its limitations, particularly in terms of brittleness and susceptibility to scratching, its advantages often outweigh these concerns, making it a go-to material for a variety of high-performance applications. As a result, it will continue to be a staple in manufacturing and design for many years to come.
FAQs
What is PMMA?
Polymethyl methacrylate, commonly known as acrylic or by brand names like Plexiglas and Lucite, is a transparent thermoplastic polymer made from methyl methacrylate monomers. It is known for its excellent optical clarity, resistance to UV light, and durability, which makes it a popular alternative to glass in various applications.
How is PMMA Made?
PMMA can be produced using either bulk polymerization or suspension polymerization. In bulk polymerization, the methyl methacrylate monomers are polymerized in a mold to create a solid, high-quality polymer. Suspension polymerization is used to produce beads of it, which can then be melted and shaped into various products. The resulting material can be cast, extruded, or molded to meet specific application needs.
Can PMMA Be Used Outdoors?
Yes, PMMA is widely used in outdoor applications due to its weather resistance and UV stability. It can withstand exposure to sunlight, rain, and other environmental conditions without degrading, which makes it an excellent choice for architectural glazing, outdoor signage, and other outdoor displays.
Is PMMA Safe for Use in Medical Devices?
Yes, PMMA is biocompatible, which means it is generally safe for use in medical devices, especially in products that come into direct contact with the body. It is used in intraocular lenses (IOLs) for cataract surgery, as well as in dental implants and bone cement. It can also be sterilized easily, which is essential for medical applications.
Can PMMA Be Colored?
Yes, PMMA can be produced in a variety of colors and finishes. It can be tinted or made in custom hues, and its surface can be textured to achieve various effects. Colored and textured PMMA is often used in signage, lighting, and decorative elements in architecture.
How Does PMMA Perform Compared to Other Plastics?
Compared to other common plastics like polycarbonate or PET, PMMA offers the best combination of transparency and UV resistance. However, it is more brittle than polycarbonate, which makes it less suitable for applications where high impact resistance is critical. Polycarbonate, for example, is more durable under extreme conditions but lacks the clarity and UV resistance that it provides.
To read more, click here